Insulated Concrete Forms: Insights from Baton Rouge Concrete Contractors
Imagine building your home with something as simple as giant, stackable blocks that add strength and save energy! Insulated concrete forms are revolutionizing construction. A guide for Baton Rouge Concrete contractors are all in on them. Let’s see why these blocks are getting so much buzz and what makes insulated concrete forms special!
What Exactly Are Insulated Concrete Forms?
Insulated concrete forms are basically “building blocks for grown-ups.” They’re made from expanded polystyrene (EPS). It is a super lightweight material used for insulation. These forms stack together to create walls. Once in place, they’re filled with concrete.
This “sandwich” design (insulation on both sides, concrete in the middle) gives homes extra insulation. That makes them ultra-sturdy and energy-saving. They provide superior fire resistance and soundproofing compared to conventional wood framing.
Top 10 Reasons Insulated Concrete Forms Are a Smart Choice
Save on Energy Bills
Insulated concrete form walls are highly energy-efficient, achieving an R-value of R-23. This is higher than most wood-frame walls. Typically maxing out around R-15. With insulation on both sides of the concrete, the walls maintain a consistent temperature.
ICFs cut down on heating and cooling needs. Studies show they cut energy bills by up to 50%. That makes them a smart long-term investment. Plus, less HVAC use means a smaller carbon footprint.
Cuts Construction Time
Insulated concrete forms can shave 2-4 months off your build time. It simplifies both exterior and interior construction. Unlike wood, which needs layers of protection from moisture, concrete doesn't rot or degrade.
ICF walls let moisture escape naturally, saving you time and hassle. So, depending on your design, the time savings can be significant.
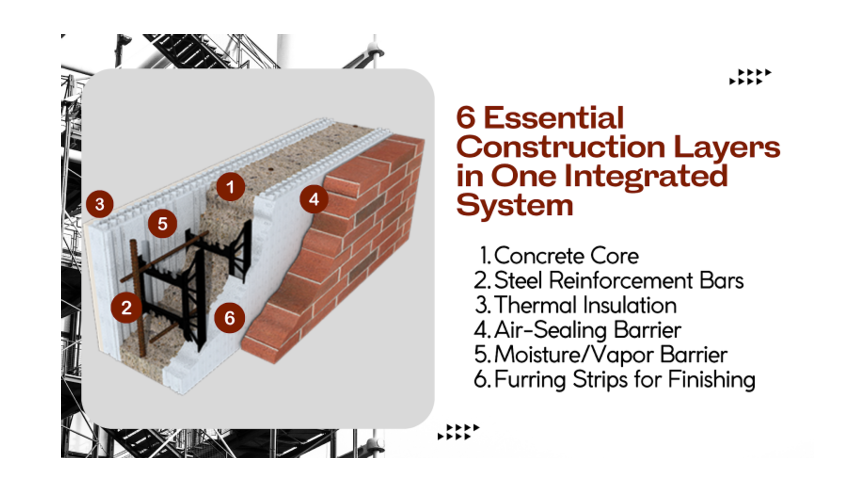
Fire and Storm Resistance
ICF homes are built to last through extreme weather and fires. In fact, one ICF home survived the 2018 California wildfires when others didn’t. They can withstand winds up to 250 mph. So they are perfect for hurricane or tornado zones.
Durability and Longevity
These homes are known as “1,000-year homes.” They last much longer than wood-frame houses. These walls resist natural wear and tear. Such as mold, rot, and pests. In fact, homes built with insulated concrete form walls can last for hundreds of years. Plus, minimal maintenance is required.
Keep Your Home Quiet
ICF construction also excels in sound insulation. Wood-frame walls have a Sound Transmission Class (STC) rating of 33-38. However, insulated concrete form walls typically have an STC rating of 54. This means that an ICF home provides a quieter living environment. They block out external noise and minimize the sound of everyday activities inside.
Environmentally Friendly Building
Insulated concrete form walls contain materials that reduce energy usage. This means a smaller carbon footprint. They’re good for your home. But they’re also great for the environment. This makes them a favorite among Baton Rouge contractors who are focused on sustainable construction.
Healthier Air Quality, No Toxins
Insulated concrete forms don’t have harmful chemicals. Like HCFCs, formaldehyde, fiberglass, or asbestos. No off-gassing either. Plus, no CFCs are used in making it.
Insulated concrete form walls create a tight seal around your home. That controls the indoor air environment.
- Cuts air leaks by 75%
- Stops dust mites
- Prevents mold
- Eases allergies like hay fever and asthma
Insulated concrete form walls are non-toxic and keep emissions nearly absent.
Net Zero
Pair insulated concrete form walls with solar tiles, and you have a net-zero home. A net-zero building is energy-efficient and runs on renewable energy. The U.S. doesn’t require new homes to be net-zero. However, the World Green Building Council is pushing for all buildings to reach this by 2050.
Build Year-Round
Concrete can be poured into ICFs no matter the weather. Your home can be built any time of year.
Lower Insurance Premiums
Insulated concrete form walls resist wind, fire, and floods. That means lower homeowner’s insurance premiums compared to traditional wood-frame homes.
Drawbacks of Insulated Concrete Forms
Insulated concrete form walls do have a few drawbacks.
- They can cost more upfront compared to traditional building methods. However, experts agree that the long-term savings on energy bills. Plus, there are lower maintenance costs that make insulated concrete forms a smart investment.
- ICFs make solid concrete walls. So adding doors or windows after the fact can be difficult. That’s why planning your floor design is critical.
- Insulated concrete form walls are typically thicker than traditional walls. That may slightly reduce the interior space of your home.
- Insulated concrete forms are a relatively new technology. It might be tricky to find experienced contractors. However, the demand is growing. So more pros are getting certified to work with ICFs every day.
Why Baton Rouge Contractors Prefer Insulated Concrete Forms
ICFs are popular with Baton Rouge Concrete Experts because they’re well-suited to local needs. Energy costs keep climbing. Plus, natural disasters are happening more often.
Homeowners want solutions that are both sustainable and strong. Insulated concrete forms provide just that. Helping homes stay cool in summer, warm in winter, and safe all year round.
Are Insulated Concrete Forms Right For You - Key Takeaway
If you’re considering a new build or even a major renovation, ICFs are worth a closer look. They offer everything. From better energy efficiency to increased durability. A smart, future-proof investment! Yes, they may come with a higher initial cost. But the long-term benefits make up for it.
Looking for pros who know insulated concrete form walls? Reach out to Baton Rouge Concrete Experts! We’ll help you build your dream home with the latest sustainable tech.